As a result of the massive developments in the apparel printing industry, Direct to Film (DTF) printing is emerging as a new frontier of innovation. The major trends that will be reshaping brands and manufacturers in 2025 revolve around sustainability, automation, advanced ink technology, and powderless printing. This article takes a look at these top DTF trends in 2025 and what they imply for the future of textile printing unless you are an print-on-demand entrepreneur, production manager, or apparel brand owner who does not need to stay ahead of such critical developments in this fast-changing market.
Sustainability & Regulatory Compliance
Sustainability has, to great effect, marked and defined priority across the textile printing industry; Direct to Film (DTF) printing has since been redefined to embrace greener approaches to environmental demands and regulations that are on the rise. Buyers no longer accept vague eco-claims; evidence of environmental responsibility, through common certifications like ISO 14001, Higg Index, Cradle-to-Cradle will be sought also compliance with international standards such as OEKO-TEX, REACH, RS will seek. Greenwashing will be cracked down on more by regulators- particularly in the EU and huge penalties imposed for misleading consumers about the environmental impact of their products. It has thus forced DTF businesses to source, label, and produce more transparently.
Waste reduction is gaining popularity, especially when stakeholders recognize that blank garment waste—often due to misprints—holds a big place in the carbon emission in DTF. To solve this problem, manufacturers and printing houses are trying recyclable PET films and bio-based adhesives which help a circular economy. These early innovations show promise in reducing the environmental footprint of both consumables and output waste. The industry is clearly pivoting toward greener, verifiable processes to align with market and regulatory demands in 2025.
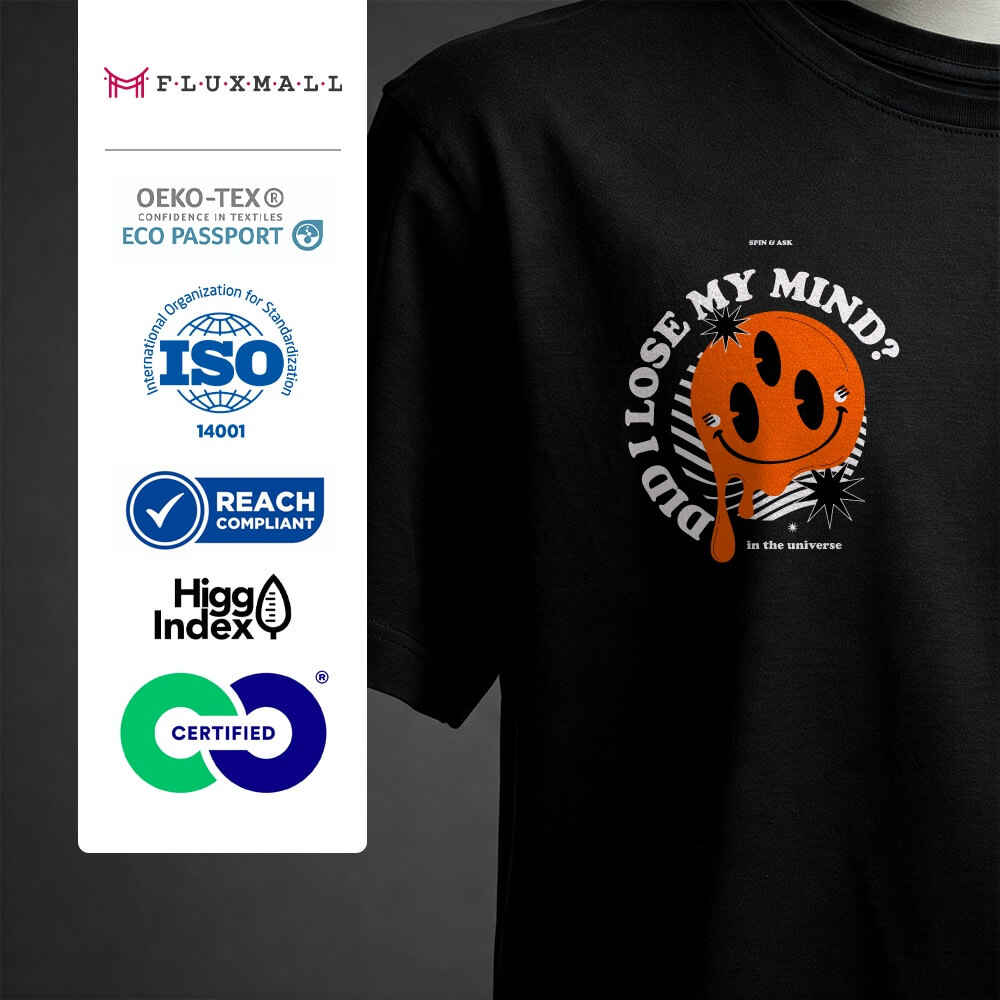
Automation & AI Integration
Productivity has turned out to be the main factor of competition in the DTF sector, while automation and artificial intelligence are helping to change workflows across all lines of production. Traditionally, the setup for pre-press, powdering, curing, and cutting had many human errors and inconsistencies. Integrated robotic workflows are solving those issues today. Factories across the globe are installing intelligent systems in which job assignments move dynamically between DTF and DTG lines using QR-code scanning as well as real-time tracking so that thousands of jobs can be handled every day with very little manual intervention.
Collaborative robots, or cobots, have taken on the repetitive job of loading and unloading garments. Throughput rates are 400-500 shirts per hour, far beyond the manual average of 50-100 per hour. In tandem, AI-driven quality control systems are being implemented to detect defects like clogged nozzles and blotches in real time, while climate monitoring systems adjust ink viscosity automatically in response to changes in temperature and humidity. This has become one of the top DTF trends in 2025.
Workflow optimization is another major advantage of AI integration. Automated nesting algorithms are helping to reduce film waste by 10–15%, and AI pre-flighting systems are now capable of flagging low-resolution artwork before it hits the printer, reducing costly errors. On the front end, AI-powered e-commerce platforms are enabling users to generate custom artwork—such as logos for schools or teams—while performing real-time intellectual property checks, creating a seamless bridge between creativity and compliance.
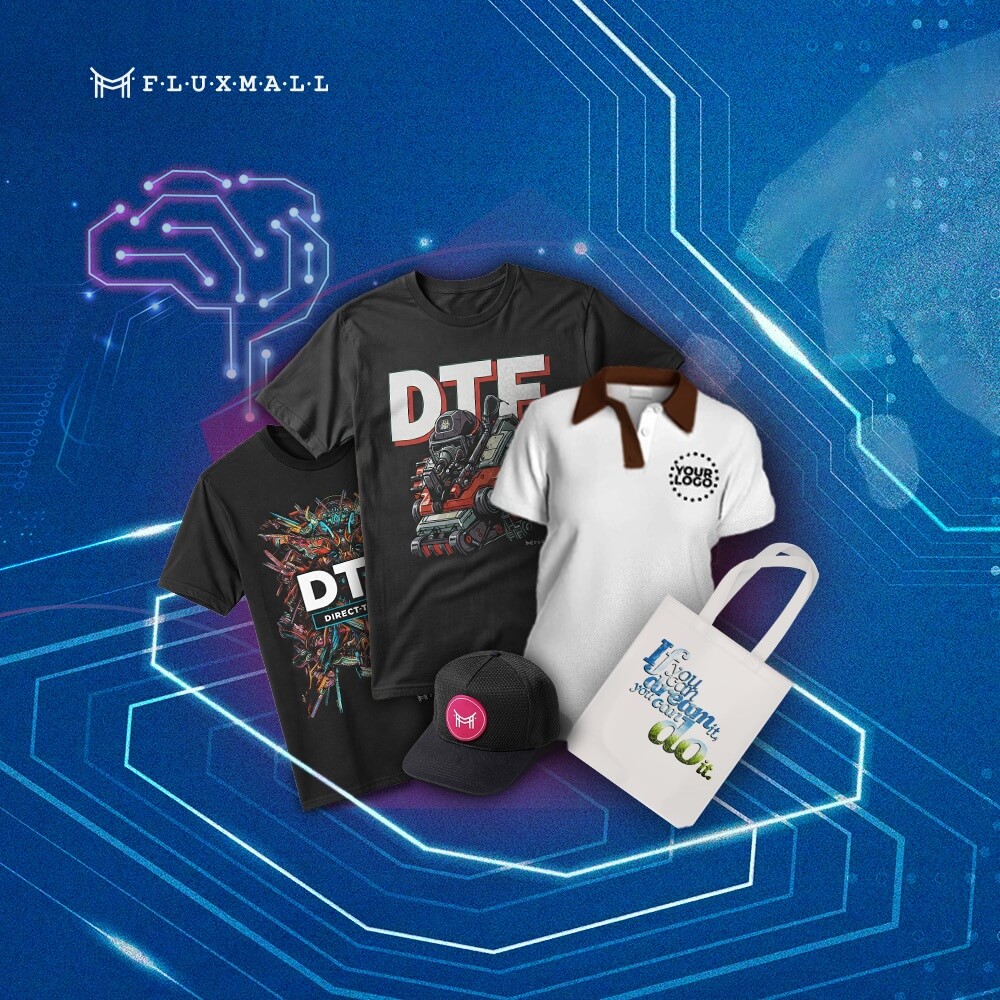
CMYK+ & Creative Inks
DTF trends in 2025 go greatly beyond the limits of usual CMYK output. Makers are bringing new ink sets like light magenta and light cyan which much improve gradients and color transitions—very key for skin tones and photo prints. Neon inks are also becoming more common for their look, giving up to 30% more brightness with color truth (Delta E <2.5) that beats standard CMYK in lots of uses.
Beside inks, metallic foils and specialty adhesives contribute to the accessibility of decorative finishes. Normally it is done by printing white ink followed by powder curing and then heat pressing the foil to achieve attractive metallic or glitter effects. Pre-textured decorative films simplify this workflow, enabling printers to produce premium finishes more easily without a major investment in new equipment.
Powderless Technology
Powderless DTF printing is among the innovations that have garnered much talk for 2025. Since these systems do not have the powdering stage, they can provide a safer and cleaner environment at work as well since operators will be safe from inhaling the powders, and also give a better hand feel to printed garments by eliminating powder residue. There is no doubt that this technology has its drawbacks. The existing powderless solutions are not very durable in terms of washing—generally, they last about 50 wash cycles as against more than 80 cycles in traditional cases. Also, because glue-based adhesives are used in powderless systems, there is higher printing head clogging which again means downtime and additional maintenance cost.
Inquiry is centering on inks which mix the adhesives into the ink itself. This would eliminate a separate channel for glue and could solve clogging problems as well while keeping the quality of printing and wash fastness. Though not ready yet, these future systems might stand for a big jump in how operations run and in safety of the product.
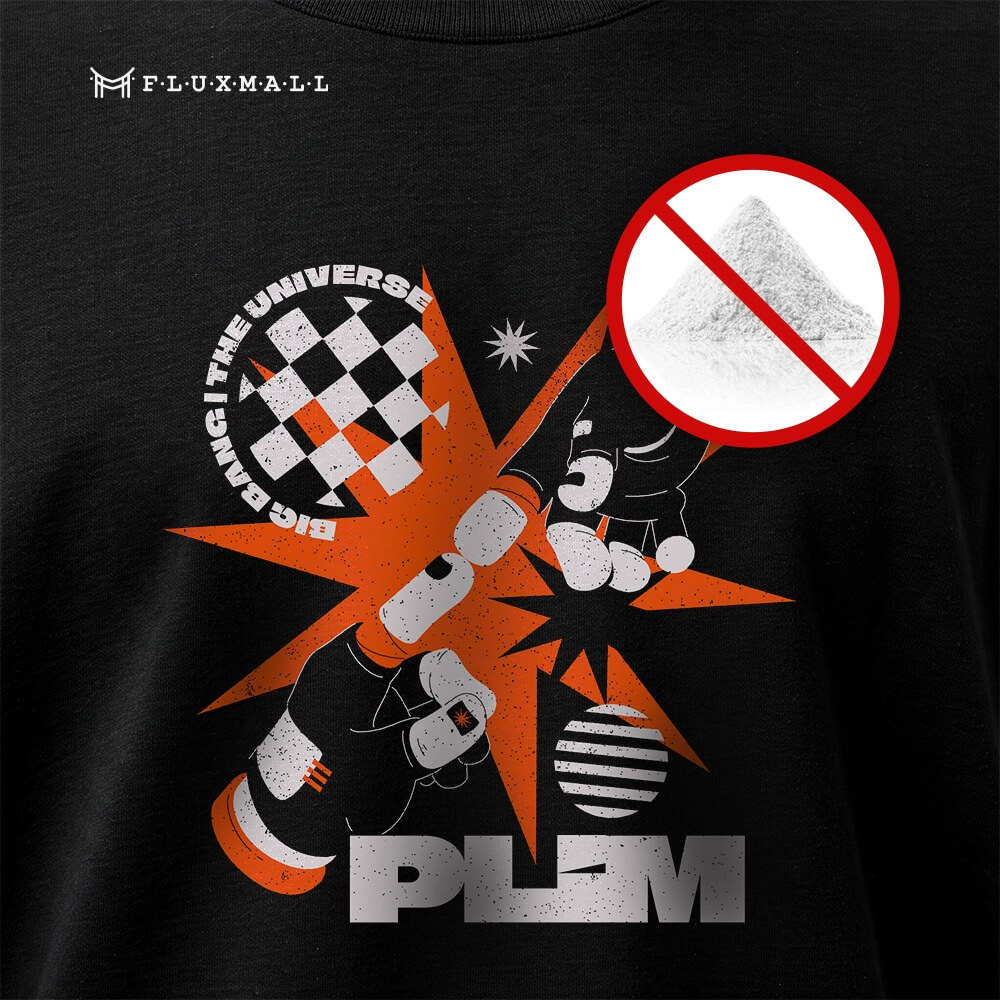