The hybrid digital printer, as a smart combination of screen printing and DTG printing, is known to be one of the most beneficial ways of garment decoration in mass-production countries. It enables the digital transformation of mid-to-large scale businesses, allowing them to adopt new technologies to maintain relevance in the market. This transformation is also a response to the changing market dynamics, where personalization and customization are becoming increasingly important to consumers. As a result, in 2024, we are likely to see more installations serving dual purposes: printing the same full-color designs in volumes and printing individual artworks for various e-commerce businesses.
What is a hybrid digital printer?
The integration of a hybrid digital printer seamlessly combines DTG (Direct-to-Garment) printing with traditional screen printing, expanding the capabilities of the screen printing press. This approach allows for the digital application of full-color artwork over the screen-printed white base, resulting in a harmonious fusion of traditional and modern printing techniques.
The combined operation of a screen printing oval machine with multiple print stations and a hybrid digital printer offers a compelling advantage in practice. This setup not only facilitates cost-effective printing but also ensures durability and high-quality output that meets the stringent expectations of the most discerning buyers. The result is a seamless and efficient process that combines the best of both worlds, delivering exceptional prints that embody both artistic finesse and lasting quality.
Advantages of hybrid digital printers
In 2024, hybrid digital printing systems will still provide garment decorators with the following opportunities:
- Substantial cost reduction associated with the white underbase.
- Flexibility to avoid pretreatment application or apply pretreatment via the screen.
- Enhanced durability and longevity of printed designs through the use of migration blockers and clear top coats.
Most popular hybrid digital printers in 2024
Oval setup for mass production: screen printing press and DTG printer
The hybrid system consists of an independent oval screen-printing machine with a variable number of pallets, which can be adjusted according to the complexity of the print and the desired output speed. The pallet count typically ranges from 24 to over 50 to meet various printing requirements. Furthermore, a DTG printer such as the Textalk TKR Series hybrid digital printer hybrid digital printer is integrated onto one of the pallets of the oval press to facilitate full-color artwork printing.
At Fluxmall we have expertise in developing factory projects based on our extensive experience with mass production factories in Vietnam and other locations. These facilities are equipped with oval presses and are dedicated to manufacturing garments and textiles for global brands. By integrating hybrid digital printers into their operations, we enable factories to handle full-color artworks with intricate details.
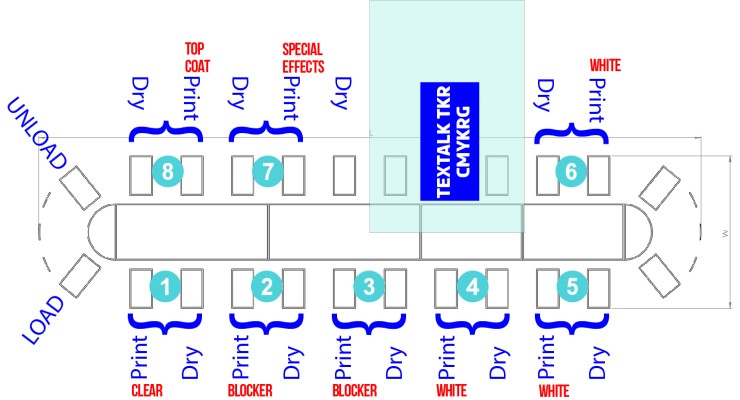
Oval setup for on-demand printing
https://www.youtube.com/watch?v=Ijh88tOvIA4
These configurations remove the need to create screens and allow decorators to print directly on ready-to-wear blank garments using customer-provided artworks.
This streamlines the production of finished products with a short lead time, meeting the market’s demand for quick turnaround. The flexibility of such hybrid systems allows for either white ink jetting via the printheads of a hybrid digital printer or screen-printed white paste solution, depending on immediate production needs. This adaptability ensures that decorators can meet different requirements, including POD. Such setups can have a combination of Textalk TFR Series hybrid digital printer to print white ink, and Textalk TGR Series hybrid digital printer to print color ink with increased resolution.
All-in-one hybrid digital printer
The aeoon Hybrid digital printer by aeoon Technologies GmbH is a compact integrated printer that combines a screen-printing station and a digital printing station, along with a flash curing system. It can be operated from a single user interface, allowing the operator to configure screen-printing settings such as the number of strokes, speed, drying after the underbase, and other parameters that influence the settings for digital printing.
This printer is suitable for smaller facilities and features an easy registration mechanism for layers compared to massive oval setups. However, the limitation of having only one screen printing station per pallet available often restricts the scope of what can be achieved. Nevertheless, this hybrid digital printer is expected to gain significant traction in 2024.
https://www.youtube.com/watch?v=gADpDLPzYo8